How to calculate inventory purchases — AccountingToolsThe ABC analysis is widely used in supply chain management and stock checking and inventory system and is implemented as a cycle counting system. It is most important for companies that seek to bring down their working capital and carrying costs. As an activity-based costing example, consider Company ABC that has a $50,000 per year electricity bill. The number of labor hours has a direct impact on the electric bill. For the year, there were 2,500 labor hours worked, which in this example is the cost driver.
How do you use ABC inventory?
ABC method of inventory control involves a system that controls inventory and is used for materials and throughout the distribution management. It is also known as selective inventory control or SIC.ABC is based on George Staubus’ Activity Costing and Input-Output Accounting. The concepts of ABC were developed in the manufacturing sector of the United States during the 1970s and 1980s. Activity-based costing (ABC) is a costing method that identifies activities in an organization and assigns the cost of each activity to all products and services according to the actual consumption by each. This model assigns more indirect costs (overhead) into direct costs compared to conventional costing. ABC Analysis is a method of tiered inventory or supplier valuation that divides inventory/suppliers into categories based on cost per unit and quantity held in stock or turned over a period of time.So there needs to be a balance between controls to protect the asset class and the value at risk of loss, or the cost of analysis and the potential value returned by reducing class costs. So, the scope of this class and the inventory management policies are determined by the estimated cost-benefit of class cost reduction, and loss control systems and processes. Inventory control is the area of inventory management that is concerned with minimizing the total cost of inventory, while maximizing the ability to provide customers with products in a timely manner.This accounting method of costing recognizes the relationship between costs, overhead activities, and manufactured products, assigning indirect costs to products less arbitrarily than traditional costing methods. However, some indirect costs, such as management and office staff salaries, are difficult to assign to a product. Inventory management and optimization in general is critical for business to help keep their costs under control.
Step ABC Inventory Analysis and Classification Process (Part 1 of 3: ABC Class Definitions)
Calculating the cost driver rate is done by dividing the $50,000 a year electric bill by the 2,500 hours, yielding a cost driver rate of $20. Activity-based costing (ABC) is a method of assigning overhead and indirect costs—such as salaries and utilities—to products and services. Since businesses are not all the same, the thresholds that define the upper and lower limits of each class are not definable.
Item C:
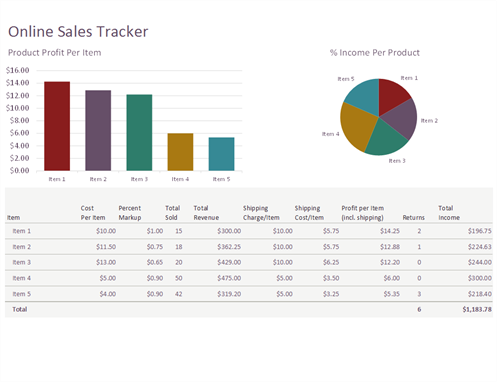
ABC classification is a simple and powerful inventory management tool that plays a vital role in inventory control and material flow planning. ABC inventory classification empowers lean manufacturers to improve the efficiency of the inventory replenishment schedule.Nor will they necessarily be fixed over time or across all locations. A business may have different risk appetites between different locations. For example, a location in a high-crime area may have a higher proportion of A items or, where a facility is less secure, more items may be classed as A.
What is ABC Method of Inventory Control?
ABC classification groups inventory items based on each item’s total annual cost. It is a straightforward task, and if you want to implement Kanban, it’s an essential prerequisite. This costing system is used in target costing, product costing, product line profitability analysis, customer profitability analysis, and service pricing. Activity-based costing is used to get a better grasp on costs, allowing companies to form a more appropriate pricing strategy. This class has a relatively high proportion of the total number of lines but with relatively low consumption values.
Join PRO or PRO Plus and Get Lifetime Access to Our Premium Materials
- Category A represents high-value and low-quantity goods, category B represents moderate-value and moderate-quantity goods, and category C represents low-value and high-quantity goods.
- Each category can be managed separately by an inventory management system, and it’s important to know which items are the best sellers in order to keep quantities of buffer stock on hand.
- ABC analysis methodology, which classifies inventory into three categories that represent the inventory values and cost significance of the goods.
What is the ABC method of inventory control?
ABC inventory system definition. The ABC inventory system is used in order to focus on the most important items in inventory. Usually a relatively few items will account for a very significant value. These relatively few items with great importance are categorized as the “A” items.ABC analysis methodology, which classifies inventory into three categories that represent the inventory values and cost significance of the goods. Category A represents high-value and low-quantity goods, category B represents moderate-value and moderate-quantity goods, and category C represents low-value and high-quantity goods. Each category can be managed separately by an inventory management system, and it’s important to know which items are the best sellers in order to keep quantities of buffer stock on hand. For example, more expensive category A items may take longer to sell, but they may not need to be kept in large quantities. Activity-based costing (ABC) is a costing method that assigns overhead and indirect costs to related products and services.The management accountant should carry out risk and stock management cost-benefit analyses by location to deliver the optimal overall cost-benefit balance and to set the ABC ranges. Due to low demand volatility, A class inventory management can usually be fully automated. And due to the predictability of demand, a low buffer inventory can be held either by the organisation itself or, in a Just In Time (JIT) arrangement, by the supplier – reducing holding costs.Fewer man-hours required.C340010%13,6002.5 weeks3,4003.5 weeksincreased safety stock from 2.5 to 3.5 weeks’ supply, delivery frequency is one quarter. Drastically reduced man-hour requirement.Total4,000100%16,0002.5 weeks5,0001.925 weeksaverage inventory value reduced by 23%, delivery frequency reduced by 69%. Overall reduction of man-hour requirement.a) A class item can be applied much tighter control like JIT daily delivery. Total delivery frequency is also reduced to half from 16,000 to 8,200.
What are the disadvantages of using the ABC analysis?
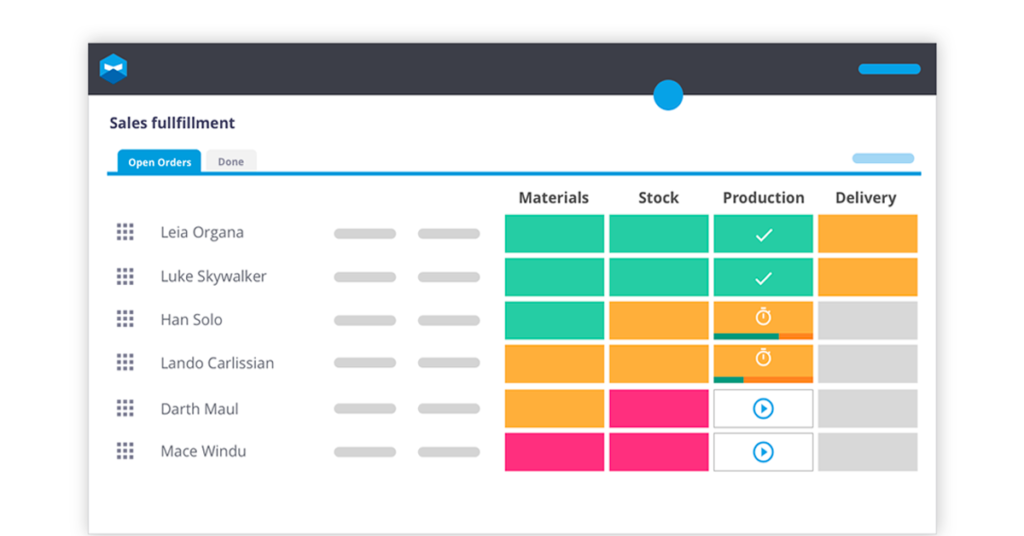
ABC analysis works towards this goal by letting management focus most of their attention on the few highest value goods (the A-items) and not on the many low value, trivial goods (the C-items). Their consumption values are lower than A items but higher than C items. A key point of having this interclass group is to watch items close to A item and C item classes that would alter their stock management policies if they drift closer to class A or class C.This is one of the four methods of overall materials management and inventory management. In inventory management, ABC analysis is an inventory categorization method used as a crude prioritization mechanism to concentrate efforts and resources on the items that matter the most for the company.
TRANSIT INVENTORY
This method is grounded in the empirical observation that a small fraction of the items or SKUs typically account for a large portion of the business. Before perpetual inventory systems became prevalent, ABC analysis was used to reduce the amount of clerical operations associated with inventory management. If you have ever heard of the 80/20 rule, there is a good chance that the person talking about it was referring to a form of ABC Analysis.
Accounting terms
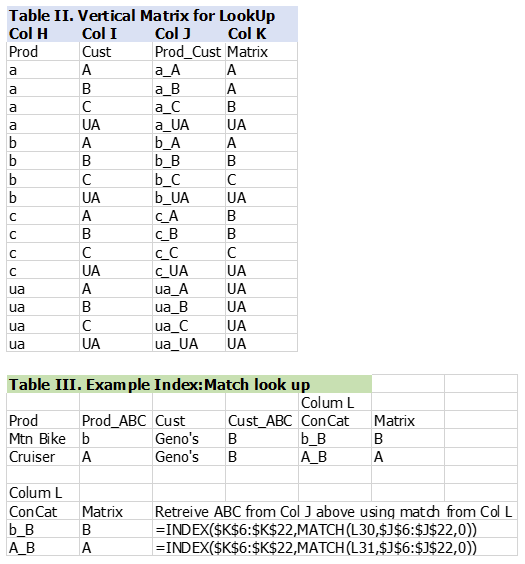
These traditional costing systems are often unable to determine accurately the actual costs of production and of the costs of related services. Consequently, managers were making decisions based on inaccurate data especially where there are multiple products.Computed (calculated) ABC analysis delivers a precise mathematical calculation of the limits for the ABC classes.It uses an optimization of cost (i.e. number of items) versus yield (i.e. sum of their estimated importance). Computed ABC was, for example, applied to feature selection for biomedical data, business process management and bankruptcy prediction. Robin Cooper and Robert S. Kaplan, proponents of the Balanced Scorecard, brought notice to these concepts in a number of articles published in Harvard Business Review beginning in 1988. Cooper and Kaplan described ABC as an approach to solve the problems of traditional cost management systems.